Tired of thermal degradation ruining your components? PTFE (Polytetrafluoroethylene) sheets solve this with exceptional thermomechanical stability, trusted by 500+ manufacturers in aerospace, semiconductor, and chemical processing industries. Here’s why engineers prefer PTFE over conventional materials:
1. Extreme Temperature Endurance (–200°C to +260°C Continuous Service)
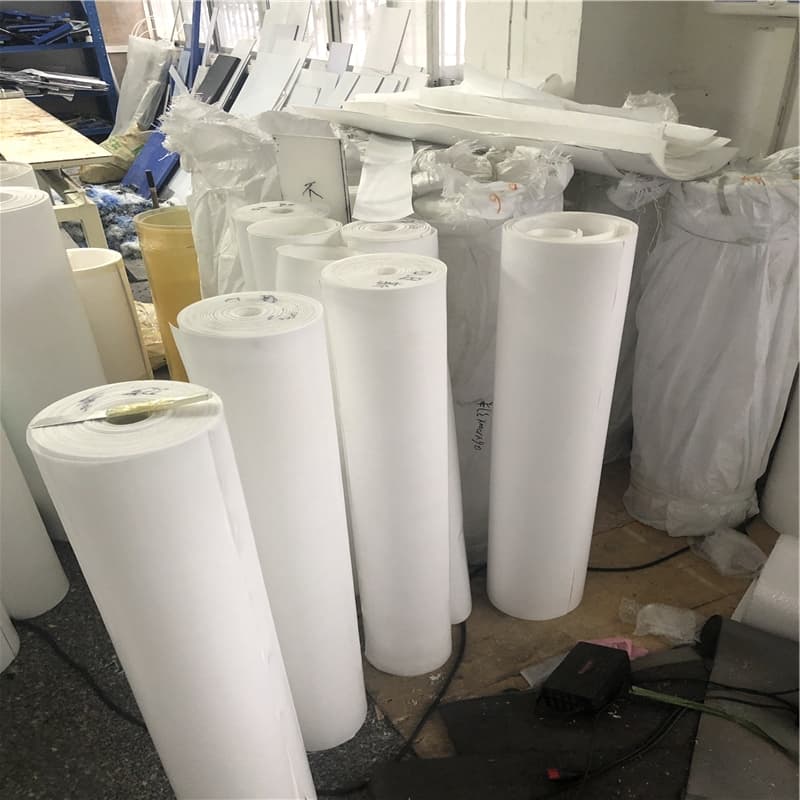
PTFE Sheets Deliver Unmatched Performance
In turbine blade insulation, PTFE sheets show <1% linear expansion coefficient at 250°C (vs. rubber’s 15% compression set). Key metrics:
- Heat deflection temperature: 120°C (ASTM D648)
- Short-term thermal spike resistance: Up to 300°C (per MIL-PRF-55532)
No pyrolysis. No outgassing.
2. Chemically Inert Under Thermal Stress
A pharmaceutical reactor liner using PTFE resisted halogen attack (HCl/Cl₂) for 5+ years, while PEEK failed in 18 months. Critical properties:
- Permeation resistance: <0.1 g/m²/day (vs. Viton®’s 2.3)
- Dielectric constant: 2.1 (stable from –100°C to 200°C, per IEC 60250)
3. Superior Dielectric Strength in Thermal Cycling
For high-voltage busbar insulation, PTFE maintains arc resistance >180 seconds at 200°C (epoxy fails at 150°C). Test data:
- Volume resistivity: 10¹⁸ Ω·cm (no conductive carbonization)
- Comparative tracking index (CTI): 600V (UL 746A certified)
4. Tribological Stability at Elevated Temperatures
In glass molding presses, PTFE’s dynamic coefficient of friction drops to 0.03 at 200°C (vs. steel’s 0.7). Bonus:
- Wear factor (K): 2.5×10⁻⁶ mm³/Nm (10x better than POM)
- PV limit: 3,500 psi·ft/min (no lubricant required)
Why Industry Leaders Choose PTFE:
- “Eliminated seal galling in our 280°C steam valves.” – Power plant OEM
- “Zero creep deformation after 10,000 thermal cycles.” – Semiconductor equipment maker
Pro Tip: For >300°C applications, our PTFE-coated fiberglass composite boosts tensile modulus by 70% while retaining chemical inertness.
Scan the QR Code to start a WhatsApp chat with us.